rotary cement kiln
Novel lime rotary kiln
The novel lime rotary kiln adopts the process of vertical pre-heater + rotary kiln + vertical
cooler. Moreover the advanced two supports technology have been introduced which can
increase greatly the kiln service life compared with the normal rotary kiln with three supports,
so it’s easy for adjust and more efficient on energy saving. The hydraulic thrust device used to
support the sliding force of whole kiln can push automatically the kiln body to move upward,
and control the sliding speed. The DCS intelligent centralized control system -most advanced
in the world is adopted to realize the unmanned operation in the production area. The kiln is
able to operate with full coal gas burning, full pulverized coal burning and coal gas & pulverized coal
blending burning in order to produce the lime of good quality.
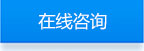
产品特点
一、Advanced structure, pre-heater and cooling system with low pressure loss
1. Most advanced vertical pre-heater is used to increase the pre-heating effect. The
decomposition rate of the pre-heated limestone ready to enter in the kiln can reach 30%.
2.Multi channel vertical cooler is used on the kiln head to quench the finished lime in order
to realize the process of “quick burning & quenching” for the lime burning.
二、 More perfect kiln production process
1. Q235-B high carbon steel made by Anyang Steel Plant is used for the kiln shell to ensure the good quality.
2. Interfaces of each section of the kiln adopt the double groove SAW welding to ensure the whole strength of the shell.
3.Annealing treatment of each section must be made after welding in order to remove the inner stress of the shell and guarantee the kiln service life.
三、High quality and suitable refractories to be applied based on burning mechanism of each section
1. At the feeding end of the kiln, since there is more abrasion and erosion on refractories we
use the high alumina refractory materials as kiln bricks.
2. At the burning section of the kiln, the basic magnesia chrome material will be used because the temperature there is very high reaching around 1200℃.
3. At the discharging end of the kiln, we will use the corundum or high aluminum refractory materials since there is increasing wear to kiln body.
四、 Four channel burner system most advanced in China
1. Large flame thrust up to 1250-1850m/s can realize the quick burning. The temperature is high but its distribution is reasonable in the kiln.
2. Special material which can be antioxidant under temperature below 2000℃ is used for the nozzles. Anti-abrasive ceramic protection layer is applied at nozzle entrance to increase
the service life.
五、 Intelligent fully automatic DCS centralized control system
1.Intelligent fully automatic DCS centralized control system is equipped.
2.Famous Siemens components and parts are used to monitor and control the whole burning system
六、 Perfect dust collection system
1. Pulse large bag dust collector with best effect will be arranged to make the centralized collection of every dust point.
2. Three stage dust collection & purifying system composed by cyclone collector + bag
collector + water film desulfurization purifier is adopted at kiln tail.
3. Dust emission concentration is <30mg/Nm3 which conforms to National Standard totally.
工作原理
1. Pre-heater, rotary kiln and cooler are key equipment for active lime production.
2. Limestone is fed first by loader in the ground silo, after vibration screening the qualified
limestone of 20-40mm are sent to the silo at top of the pre-heater by feeding belt conveyor.
3.After entering into the pre-heater, the limestone absorbing the heat from the exhaust gas move
reverse with air stream. The independent pre-heater can make the full heat exchange between
limestone and materials, decreasing thus the temperature of waste gas to 280℃ below.
4. The limestone calcination is completed in the kiln. The materials which move axially & radially
are always in roll state, and the three heat exchange modes namely radiation, convection and
conduction are carried out simultaneously so that the whole calcination process is very uniform.
5. After calcined the limestone is sent to the vertical cooler. The secondary air blasted from the
bottom of the cooler is used for cooling the limestone. The independent cooling equipment
whose tubes are arranged uniformly on entire section can cool the limestone under 100℃ below.
The secondary air after heated up enters in the kiln to participate in combustion. The cooled
lime is discharged out uniformly through the vibration feeder.
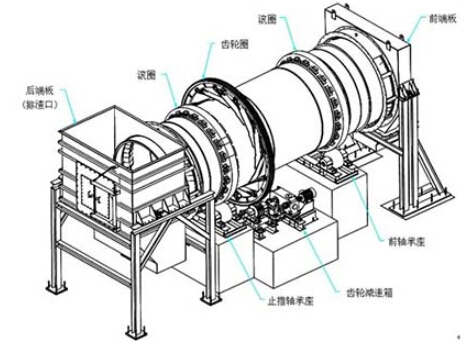