electrolyte cleaning and grind
1. Aluminum Oxide Crust Grindding System
This system was researched and developed by my company accordance with the demand of the present domestic electrolyte industry. We own the innovation and independent intellectual property right. The system can be used as three kinds model on the basis of different product size. Now the system has been in operation, and already got the praise by users. This system improved the original from multi-stage crushing system to the first-stage crushing. Through the adjustment of internal equipment system to meet user’s different capacity and size requirements. The system can realize intelligent control and save the manpower cost. The system has internal dedusting equipment, which can realize the dust purification.
Main equipments: Jaw crusher, grinding machine, bucket elevator, vibrating screen, bag-type dust collector, dust fan
2. Screening and grinding system
Base on the successfully used of the alumina crust grinding system and final product granularity of 4~20mm, our company improved and patented this new screening and grinding system. This system integrate screening with grinding. It is simple, low cost, high efficiency, large production capacity.
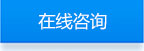
产品特点
Features
1、This system improved the original from multi-stage crushing system to the first-stage crushing. Through the adjustment of internal equipment system to meet user’s different capacity and size requirements.
2、The system can realize intelligent control and save the manpower cost.
3、The system has internal dedusting equipment, which can realize the dust purification.
工作原理
working principles
The open cycle system for 200 mesh material powder
Step 1: Transmit the electrolyte on the residual surface into the jaw crusher for primary crushing, and the big one will be transmitted to the surge bunker with the help of the belt conveyor.
Step 2: The vibrating feeder uniformly send the material to the grinding machine for crushing and grinding, then come into the classifier through the fan for sizing.
Step 3: The granule that required will be collected in the bag-type dust collector, and those not required will go back to the grinding machine for further grinding with the help of the centrifugal force.
Step 4: The negative pressure that produced by the fan make the dust come into the bag-type dust collector, and finally into the finished hopper. And the gas that meets the environment will be discharged directly into the atmosphere.